In a world racing toward cleaner fuels, discover the hidden component making LNG transport safer, leaner, and greener—Vacuum Jacketed Valves.
The Cryogenic Backbone of LNG Infrastructure
As global energy pivots towards cleaner alternatives, Liquefied Natural Gas (LNG) has emerged as a crucial transitional fuel. Yet behind the high-profile terminals, tankers, and megaprojects lies an overlooked but essential player: the vacuum jacketed valve (VJV). Designed to operate under extreme cryogenic conditions, these valves are not just components—they’re enablers of operational reliability, safety, and cost-efficiency.
In LNG ecosystems—from export terminals and FSRUs to bunkering stations and regasification plants—every element must perform flawlessly at -162°C. That’s where vacuum jacketed valves quietly outperform their unjacketed peers. Yet their role is still underappreciated.
What Makes Vacuum Jacketed Valves So Vital?
Unlike standard cryogenic valves, vacuum jacketed valves feature an insulating layer that dramatically reduces heat ingress and eliminates external condensation. This isn’t just about performance; it’s about preserving product integrity, minimising boil-off, and ensuring operator safety.
- Thermal insulation: The vacuum jacket prevents heat from penetrating the valve body, maintaining cryogenic temperatures throughout.
- Zero ice formation: Operators avoid dangerous frost or ice buildup on external surfaces.
- Minimised boil-off gas (BOG): With reduced heat leakage, LNG boil-off is kept within design limits, reducing waste and re-liquefaction load.
- Extended equipment life: Reduced thermal cycling and mechanical fatigue extend the lifespan of piping and ancillary systems.
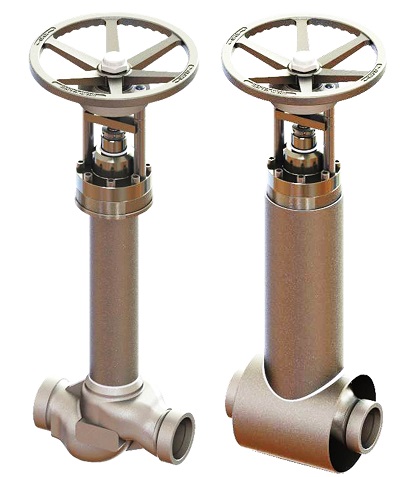
For terminal operators and EPC contractors, this translates directly to lower total cost of ownership and improved safety profiles.
Blackhall Engineering’s Contribution: Innovation in Every Weld
With over half a century of cryogenic valve expertise, Blackhall Engineering has consistently led innovation in harsh environments. Our vacuum jacketed valves—Series 2027 (Non-Bellows Sealed) and Series 2028 (Bellows Sealed)—are the definitive answer to the challenges of LNG, industrial gases, and hydrogen applications.
Series 2027 – Non-Bellows Sealed
Designed for applications where maintenance access is routine and emissions are less critical, Series 2027 valves are robust, versatile, and efficient. Their design simplifies integration into modular skids and fixed LNG terminals alike.
Series 2028 – Bellows Sealed
For applications involving hazardous or high-purity gases—like hydrogen or oxygen—Series 2028 provides zero-emission, hermetically sealed reliability. Certified to meet stringent leakage requirements, it exemplifies Blackhall’s “Valves for Life” philosophy.
Every Blackhall vacuum jacketed valve is CFDA and FEA validated, helium-tested in our cryogenic clean rooms, and compliant with international gas and marine classification standards—from DNV to Lloyd’s Register.
Market Dynamics: Why LNG and Hydrogen Need VJVs Now
According to McKinsey & Company, global LNG demand is expected to grow by over 50% by 2040. Emerging economies in Asia, Europe’s drive for energy diversification, and maritime decarbonisation efforts all reinforce LNG’s critical role.
Simultaneously, the hydrogen economy is gathering pace. The EU alone is investing €30 billion in green hydrogen infrastructure, where cryogenic handling is mission-critical. Both sectors demand flawless thermal management—and that’s where VJVs are irreplaceable.
As plant managers and system engineers know, LNG and liquid hydrogen are unforgiving: even minor thermal ingress can cause costly vapour lock, increased BOG, or—worse—system shutdown. Vacuum jacketed valves, especially Blackhall’s, mitigate these risks at the source.
The Valvologist® Approach: Engineering Longevity
At Blackhall, our approach is rooted in Valvology®—the science and art of building valves with character, purpose, and durability. Every valve is engineered not just for compliance, but for performance over decades. It’s why our customers include the world’s leading gas producers, hydrogen pioneers, and LNG majors.
In a sector obsessed with lifecycle costs and environmental stewardship, Blackhall vacuum jacketed valves offer a distinct competitive advantage—technical excellence, British craftsmanship, and support that extends far beyond delivery.
Applications Across the LNG Value Chain
Vacuum jacketed valves are found wherever cryogenic fluid handling is critical:
- LNG export and import terminals
- Floating Storage Regasification Units (FSRUs)
- Hydrogen liquefaction and dispensing systems
- Industrial gas separation and filling plants
- Marine bunkering infrastructure
Their benefits compound across each segment—improving uptime, enhancing safety margins, and reducing boil-off losses.
Procurement with Purpose
For procurement specialists, the move toward reliable, high-performance cryogenic solutions must be paired with partners who can support design, testing, and long-term service. Blackhall doesn’t just sell valves—we provide certainty.
Our cryogenic valve clinics, in-house R&D, and long-term refurbishment programmes allow operators to extract maximum value across the valve’s lifecycle—whether in a mega LNG terminal or a compact modular hydrogen unit.
Learn more about our LNG valve range here.
Final Thoughts: Valves That Don’t Just Function—They Lead
Vacuum jacketed valves may be invisible to the untrained eye, but for those building the future of LNG and clean energy, they are mission-critical. As project scopes grow and tolerances shrink, only those who prioritise performance, sustainability, and longevity will thrive.
At Blackhall, we’re proud to engineer not just valves—but solutions that carry the future of energy safely and efficiently. Get in touch to explore how our Series 2027 and 2028 VJVs can elevate your next cryogenic project.
Contact us today on +44 (0) 1484 407080 or
FAQs: Addressing Common Queries on Vacuum Jacketed Valves
How do vacuum jacketed valves differ from standard cryogenic valves? Standard valves lack thermal insulation, making them vulnerable to heat ingress and external frosting. Vacuum jacketed valves use a vacuum-insulated sleeve to eliminate heat transfer, which is essential for cryogenic applications where temperature stability is non-negotiable.
Do vacuum jacketed valves increase CAPEX? While initial costs may be higher, the long-term operational savings in reduced boil-off gas (BOG), extended component life, and lower maintenance result in substantial reductions in Total Expenditure (TOTEX)—especially when supplied by Blackhall Engineering with lifecycle support included.
Are Blackhall VJVs suitable for hydrogen applications? Absolutely. The Series 2028 Bellows Sealed VJV is particularly suited for hydrogen, offering zero leakage and high-integrity sealing in the most demanding purity and safety applications.
How do Blackhall valves support sustainability goals? Through initiatives like the Renov8 programme, we help clients reduce carbon footprints by offering repair and refurbishment options that avoid unnecessary imports and manufacturing emissions. Coupled with ultra-low leakage and long-life design, our valves help clients meet environmental KPIs and regulatory targets.
Client Success Snapshot: Trusted by LNG Leaders Worldwide
Blackhall Engineering valves have been deployed in over 80 countries, including high-profile LNG and industrial gas infrastructure in the USA, Asia-Pacific, and the Middle East. Our components are often mission-critical in:
- Floating LNG production units (FLNGs)
- Green hydrogen liquefaction sites in Europe and Asia
- ASU (Air Separation Units) for multinational gas giants
In one recent installation, Blackhall VJVs helped a LNG terminal reduce thermal ingress by 78%, cutting boil-off by over 12 tonnes/month—a result that paid for the valve upgrade in under 18 months.
Integrated Digital Engineering for a Smarter LNG Future
What truly sets Blackhall apart is our commitment to intelligent engineering. Using Finite Element Analysis (FEA), Computational Fluid Dynamics (CFDA), and Seismic Modelling, our valves are optimised not just for today’s applications, but for tomorrow’s risks.
For LNG terminals adopting predictive maintenance regimes, our valves come integrated with IoT-readiness, enabling monitoring of leakage, actuation cycles, and temperature gradients via the ValveMetrix® platform.
Next Steps: Specify Vacuum Jacketed Valves with Confidence
For engineers, procurement teams, and project developers navigating the shift towards cryogenic infrastructure, choosing the right valve supplier is not just about price—it’s about trust, support, and performance in the most extreme conditions.
With Blackhall Engineering, you gain more than a product. You gain a strategic partner in performance. Contact our team to:
- Request a Series 2027/2028 VJV datasheet and 3D CAD files
- Schedule a technical consultation with a Valvologist®
- Book a factory or virtual tour of our testing facilities
Whether you’re retrofitting an existing LNG plant or designing a new hydrogen corridor, Blackhall vacuum jacketed valves will be your strongest asset.
Ready to Lead the Future of Cryogenic Reliability?
Join a growing list of global leaders in energy, industrial gases, and hydrogen who rely on Blackhall for critical cryogenic infrastructure. Our cryogenic valve portfolio is a testament to our legacy—and a promise for the future.
Let’s design a safer, smarter LNG future—together.
☎️ +44 (0) 1484 407080